MINING AUTOMATION
Innovation towards autonomous mining
The current context in the mining sector, with raw material prices at record highs, but at the same time volatile, has led large companies to rethink the current production model. The answer is the incorporation of new technologies, taking increasingly firm steps towards digital transformation. This path towards a technological maturity that other sectors already have is a complicated process and sometimes full of barriers specific to the sector.
Zitrón, a company with a clear vocation for innovation, presents its intelligent ventilation management system for mining. The objective of the system is the optimization of ventilation in mines, resulting in a significant improvement in the working conditions of miners and a decrease in the energy consumption of mines (up to 40%), which sometimes represents the highest energy cost that mines have.
The rationale is to direct air where it is needed and in the volume that is needed, to have safer working conditions, to increase productivity and to reduce energy consumption. All this translates into a faster return on investment due to energy savings, reduced carbon emissions and greater guarantees in both safety and system reliability.
Thus, starting from several complex 3D representations of ventilation circuits that offer information that is difficult to manage, Zitrón is committed to an agile, simple and useful system.
Fig. 1: Zitrón monitoring system. Control panel showing the ventilation system of a mine in southern Europe.
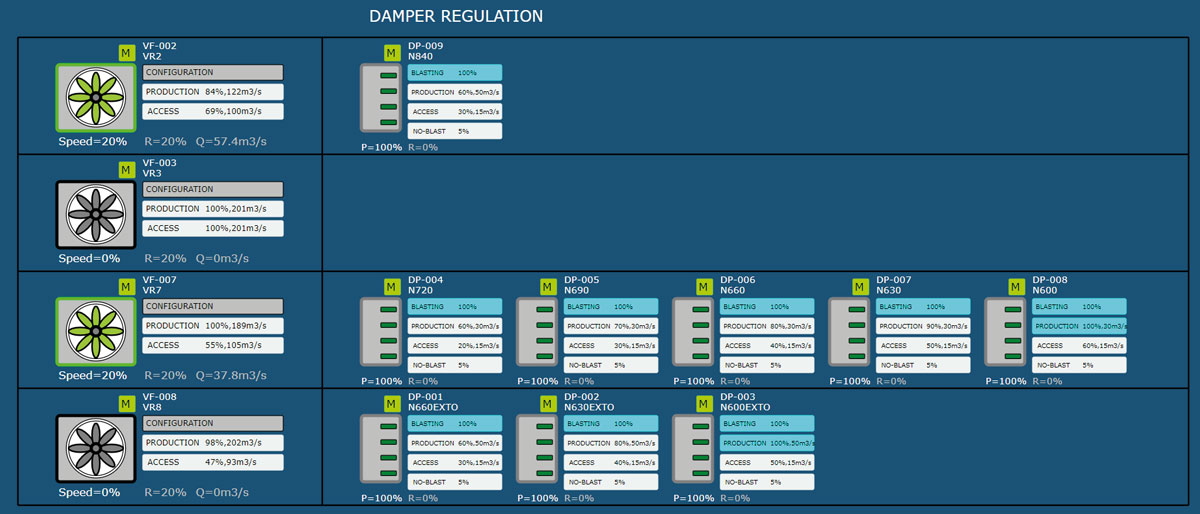
Fig.2: Representation of the control system of the main equipment, dampers as a function of the ventilation requirements at each production level (mine in southern Europe).
Implementation process of the intelligent ventilation management system.
In most mines around the world, ventilation is not correctly sized. It is necessary to analyze the actual airflow needs to know if the ventilation system is optimized, otherwise the mine could miss out on many opportunities for improvement. The result of such an analysis is the most important aspect at the moment of planning. It is not only about providing the necessary flow, but also about getting it to the place where it is needed at any given moment, as it is not always necessary to have the maximum flow in the mine. This will depend on the tasks being performed and the location in the mine where they are being carried out. It is essential to measure in order to optimize.
Zitron’s team of mining experts has been the basis for the development of this system. Their solid knowledge of ventilation systems in mines is combined with their mastery of the different mining methods that exist in mining. This allows the management and monitoring system to be adapted to the real needs of each mine in an efficient and effective way. In order to do this, an exhaustive analysis of the primary and secondary ventilation systems is carried out, obtaining the main ventilation KPIs, which become the necessary indicators to optimize the system, in order to subsequently design an automation plan adapted to each mine. This is materialized in a control and monitoring software of the ventilation in real time, being able to implement saving strategies according to the type of mining.
The system offers a total integration solution that can start from the installation of any type of communications system or can be adapted to the existing one. It is flexible, simple and practical, and its implementation can be done in phases, collecting in real time all the parameters of the equipment that make up the system (main fans, dampers, auxiliary fans, etc.).
Another advantage is the possibility of predictive maintenance, which in turn will reduce OPEX and CAPEX costs of critical equipment, minimizing the problems of catastrophic failures (Fig. 3 and 4).
The elements that make up the real-time monitoring system and that are integrated in the fans, dampers, gas stations, etc., have been designed and manufactured by Zitrón’s R+D+i department, complying with the highest quality standards.
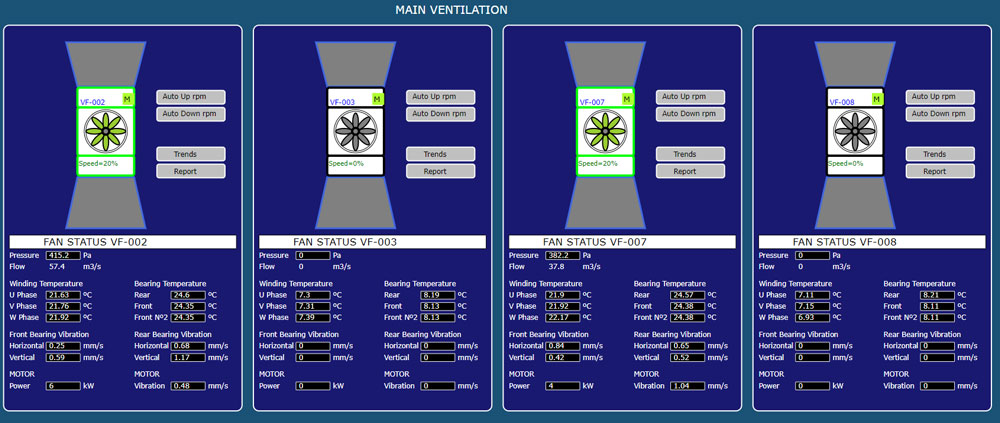
Fig.3: System control screen for the main fans
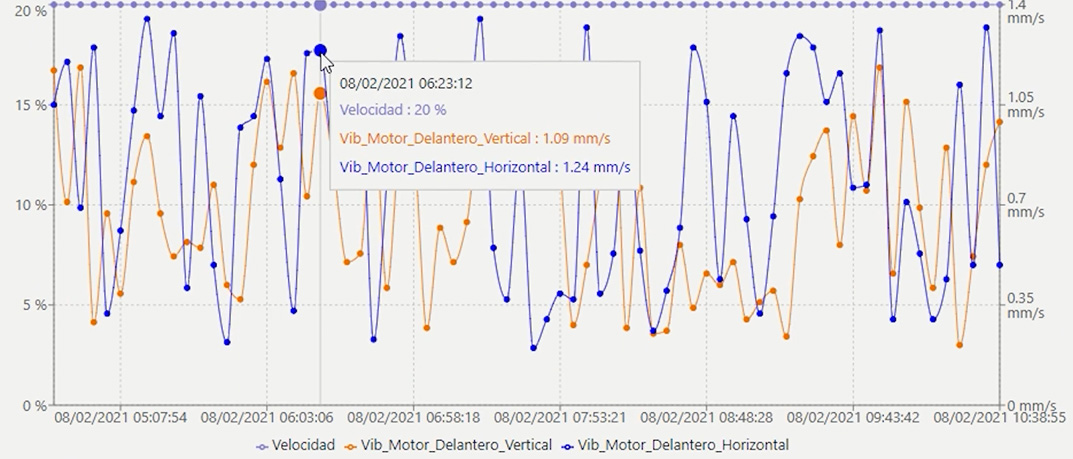
Fig.4: Trend analysis panel of the parameters collected from the main equipment.